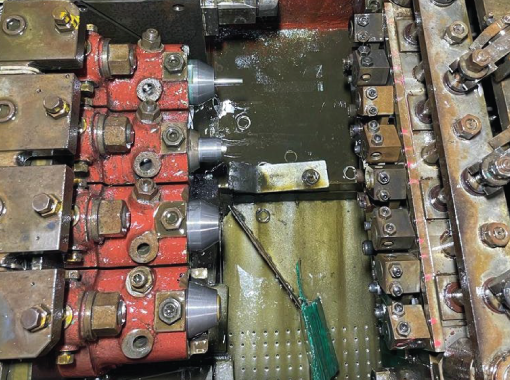
COLD FORMING
We manufacture special cold-formed and machined components and work closely with our customers to design products and processes that are best suited for their application. Our extensive cold-forming capabilities range from 6mm to 20mm in diameter, and 15mm to 240 mm in length. The materials we currently work with include carbon steel, alloy steel, stainless steel, aluminum, copper and brass. We have a battery of multi-station cold forming machines from renowned manufacturers such as National, Hatebur, Jyoto and Waterbury Farrell.
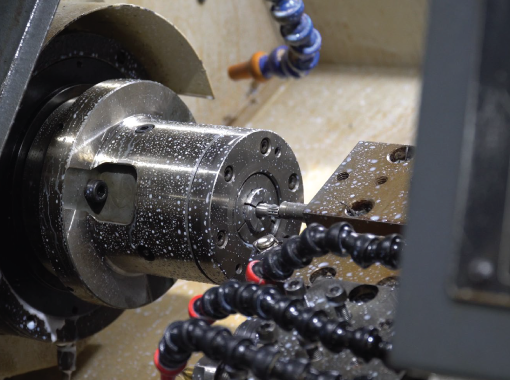
MACHINING AND SECONDARY OPERATION
The forging blanks are finish machined on a wide variety of secondary operation machines. Our machine shop has 26 CNC lathes, centreless and cylindrical grinding machines, circular and flat thread rolling machines, Wickman multi-spindle lathes, Drilling and tapping machines and a variety of special-purpose machines that are used for manufacturing high-volume components.
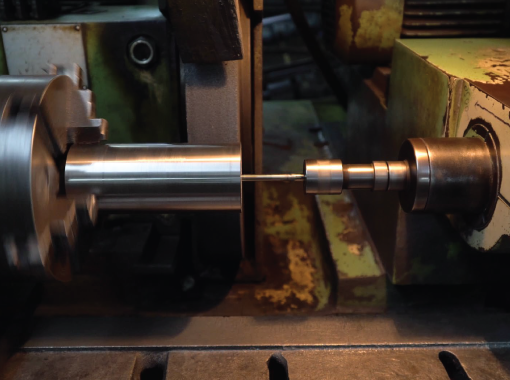
DEDICATED TOOL ROOM
Our in-house dedicated tool room is equipped to manufacture all the critical tools that are required for our manufacturing process. The machinery list includes lathes, cylindrical and surface grinding machines, milling machines, tool and cutter grinding machines and lapping machines. We also have dedicated vendors for critical operations such as spark erosion, CNC wire cut, high-performance surface coating and tool steel heat treatment. We work closely with a number of specialty tool manufacturers to source the best quality carbide tools.